Crack prevention in concrete: New 3D printing method inspired by ancient Fish
Researchers at Princeton developed a new concrete design inspired by coelacanth scales, using advanced 3D printing to create a double-helix structure that resists cracking 63% more than traditional concrete. The method, featuring a two-part extrusion system and robotic precision, enhances durability and shape retention.
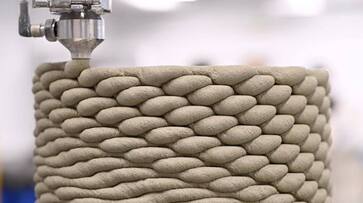
Concrete is a common material used in construction, but it can develop cracks over time. To make sure that concrete structures last a long time and remain safe, it's important to prevent or reduce cracking.
Researchers have created a new method to make concrete last longer by enhancing its ability to resist cracking and breaking. This approach focuses on improving the concrete's strength against fractures, helping it stay durable for a longer time. The engineering team at Princeton used advanced 3D printing techniques and precise robotic technology to make twisted concrete parts. The new concrete produced is stronger and lasts longer than regular cast concrete. Interestingly, it has 63% more resistance to cracking compared to standard concrete.
Inspired by nature's design (or architectural design), the researchers sought to apply similar ideas to enhance the crack resistance of concrete. They took inspiration from the double-helix-shaped scales of the coelacanth, an ancient fish species. These natural structures are renowned for their durability and ability to resist cracking.
The coelacanth is an ancient type of fish, and its scales are shaped like a twisted ladder, similar to the double-helix shape of DNA. This unique design makes the scales very strong and able to resist breaking easily. The researchers developed a new concrete design inspired by the structure of coelacanth scales. They utilized a robotic printer to build a 3D structure by stacking individual strands of concrete.
"Individual strands" means thin, separate pieces or layers of concrete that are laid one at a time to form the overall structure. It's like building something piece by piece rather than pouring it all at once. One of the main design features was the double-helix structure. This means that the strands were arranged in two layers, twisted around each other, much like the shape of a DNA molecule.
This design made the material more resistant to breaking. If a crack starts to form, the twisted structure could help stop it from growing or spreading further. The article describes the material's ability to resist crack growth as a strengthening method, and the information was shared by Interesting Engineering.
The method uses several strategies to either block cracks from spreading, lock the broken surfaces together, or divert cracks from following a straight path once they appear, as the authors explained in the press release.
Constructing these detailed structures requires the precise control that robotic manufacturing offers. Thanks to advancements in additive manufacturing, researchers have now been able to create complex shapes that were once hard to make using traditional casting methods.
The Princeton facility features large industrial robots equipped with cutting-edge real-time material processing tools. This allows researchers to produce full-size structural parts that are not only practical but also visually attractive.
Advanced real-time material processing tools refer to high-tech equipment that can manipulate and shape materials instantly while being monitored and adjusted in real time. This enables the precise and efficient production of parts and structures during manufacturing.
In addition to this progress, the team developed a new technique to stop fresh concrete from losing its shape during the 3D printing process. They used a "two-part extrusion system" that combined concrete with a chemical accelerator right before the printing process.
This method sped up the hardening of the concrete and kept it from sagging under its weight.
A two-part extrusion system is a process where two materials, like concrete and a chemical additive, are mixed right before being shaped or printed, ensuring better strength and stability.
An accelerator is a chemical added to materials like concrete to make them harden or set faster than usual. It accelerates the solidification process. The press release stated that by carefully adjusting the amount of accelerator, the researchers were able to better control the structure and reduce deformation in the lower layers.
This breakthrough could improve the construction industry and lead to the creation of stronger, longer-lasting structures in the future.

